Why Choose Single Component Polyurethane Over Multi-Component Materials?
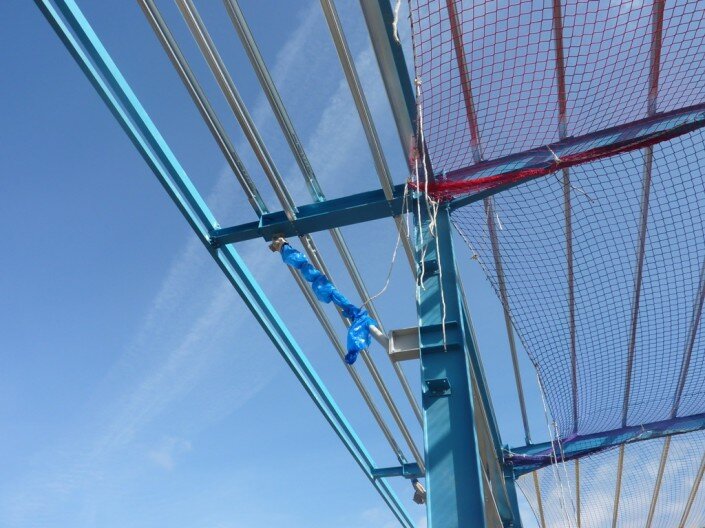
Single component polyurethanes are more technological in comparison with two-component epoxies and polyurethane compounds. Cured due to moisture in the substrate and the surrounding atmosphere, single component polyurethanes solve the problem of corrosion protection way more effectively, eliminating the underlying cause of corrosion under the coating film through using the moisture adsorbed on the surfaces for its polymerisation.
Epoxy resins and alkyd paints retain or block the moisture under the cover and in the pores of the substrate. This moisture will expand during freezing, causing a loss of adhesion of the epoxy resin or an alkyd varnish and blistering and peeling of the old paint layer with subsequent complete loss of its function. As for moisture-curing polyurethane materials, the fact should be underlined that they capture and remove moisture from the layer of rust and absorb atmospheric moisture to cure and create a holistic anti-corrosion coating with high adhesion to the surface. Thus, there is no integrity destruction danger during freezing and thawing of the anti-corrosive coating because of absence of moisture under the cover.
Single polyurethane coatings: spheres of application
Due to the impressive lifecycle of anticorrosion coatings, from 5 to 15 years and above, the materials are used for corrosion protection in a sweeping variety of industries, including:
- Oil (tanks, pipelines, pumping stations, machinery and equipment)
- Roof waterproofing, reinforcing, roof coating
- Shipbuilding (underwater parts of ships and superstructure, port facilities, offshore platforms)
- Chemical (reactors, tanks, equipment)
- Mountain ( tunnels , sewers , machinery and equipment)
- Construction and repairing (bridges , highways, buildings)
- Water management and wastewater treatment
- Ferrous and nonferrous metallurgy; mechanical engineering
Polyshield coating under the microscope
Polyshield is produced in a good number of variants with various properties of the resulting coating and its waterproofing capabilities in particular. The materials are used in laying new or repairing old roofing and metal coatings for protection from UV exposure and mechanical destruction of polyurethane thermal insulation coatings on walls and roofs of buildings and structures. As stated by Britannia Paints, a seasoned roof waterproofing business players with 10+ years of successful track record, polyshield is an ideal roof coating material, oftentimes applied to the screed, pool, septic tank and reservoir systems.
With impressive strength characteristics and abrasion resistance finds its application in waterproofing the components designed to sustain heavy loads (bridge structures and overpasses) and subjected to extreme conditions (that’s why Polyshield is implemented in roof waterproofing projects). The material is also utilised in building water treatment plants, tunnels, underground garages, parking lots and sumps.
Due to their unique properties and qualities polyurea Polyshield most effective and sometimes the only material for waterproofing works in construction.
- Maintains elasticity in a wide temperature range (from -50 ° to +150°c)
- Lasts long (50+ years)
- Offers excellent adhesion to concrete, steel, rolled materials
- Represents seamless waterproofing fabric
- Provides high mechanical strength and abrasion resistance
- Boasts extremely high resistance to abrasion
- Contains no solvents and plasticisers (completely odorless)
- Performs the function of the dielectric, preventing sparking
- Has a high temperature resistance (-50°C to +150°c)
- Resistant to oil products, wastewater and most of the chemical reagents
Even though construction professionals are far from the idea that Polyshield is called into being to replace all the currently existing waterproofing materials, they are confident that the future inevitably belongs to the neoteric material that guarantees decent waterproof results on large areas in no time.